
An artist’s impression of the SpaceX Starship beginning its descent over Mars. Image: SpaceX.
It’s been a year since SpaceX CEO Elon Musk unveiled the prototype of Starship, which is a two-stage fully reusable rocket the company hopes to use for interplanetary missions. Since then, and after a series of tests, SpaceX has reported that it is ready to conduct Starship’s first test flight, specifically of prototype serial-number 8 (SN 8).
That reusability reduces costs is self-explanatory. Musk famously said in 2014 that a fully reusable mission could reduce the cost of space travel by a factor of 100. SpaceX was established with the long-term goal of colonising Mars, so Starship as such marks the company’s most important development to date. Reusability is a central feature of this project, after SpaceX perfected it with over two score flights of its partly-reusable Falcon 9 rocket.
And in the last couple days, SN 8’s landing manoeuvre has been the subject of many conversations among spaceflight enthusiasts online.
SN 8’s structure is made of an alloy called 304L, along with some other alloys of stainless steel. The chassis is augmented with a nose cone and aerodynamic surfaces. (Neither Musk nor SpaceX have said anything about Starship’s reactionary-control and torque-control systems, which govern the vehicle’s attitude and torque, respectively.)
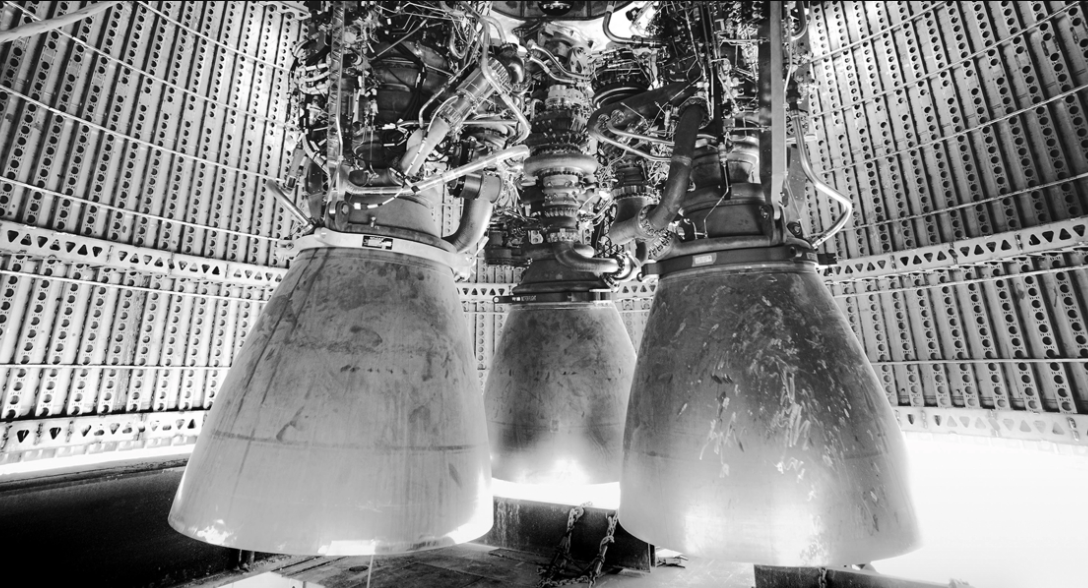
Earlier this year, SpaceX test-flew the SN 5 and SN 6 prototypes about 150 metres up and back down. These prototypes lack the nose cone and other features of SN 8 – looking more like grain silos – and SN 8’s test flight will be up to 15 km. To power these vehicles, SpaceX has developed a methane-fuelled engine called the Raptor, which can generate a thrust of 2,200 kN at a chamber pressure of 330 bar. To compare, the CE-20 ‘high-thrust’ cryogenic engine the Indian Space Research Organisation is developing for the GSLV Mk III rocket has a thrust of 196.5 kN at a chamber pressure of 60 bar.
The Raptor is a staged rocket engine fuelled by cryogenic methane and liquid oxygen (a combination referred to as methalox). Among other reasons, the choice of fuel was motivated by the fact that both methane and liquid oxygen can be obtained on Mars’s surface after some processing. The Starship is expected to be equipped with three Raptor engines, for a total thrust of 6,600 kN to lift this vehicle. SpaceX is also developing another big rocket, called the Super Heavy, expected to be fit with over two dozen Raptor engines.
During the test flight, SN 8 will be expected to rise up to 15 km before beginning its slow descent (it isn’t fit with heat shields). The landing event will be unique because SN 8 will use a belly-flop manoeuvre – for the first time in the history of spaceflight. SpaceX has said this manoeuvre could reduce the vehicle’s fuel expense.
SN 8 will first free-fall towards its landing point in a horizontal position. Its engines will remain ‘off’ while the vehicle descends to the ground at 60-70 m/s. Its descent will be controlled by the vehicle’s aerodynamic surfaces, especially the rear and front body flaps, which will also work like air-brakes. They will be part of a closed-loop control system, of the sort that missiles use to follow pre-programmed trajectories. They will be controlled by electric motors instead of by hydraulic systems, which is also novel.
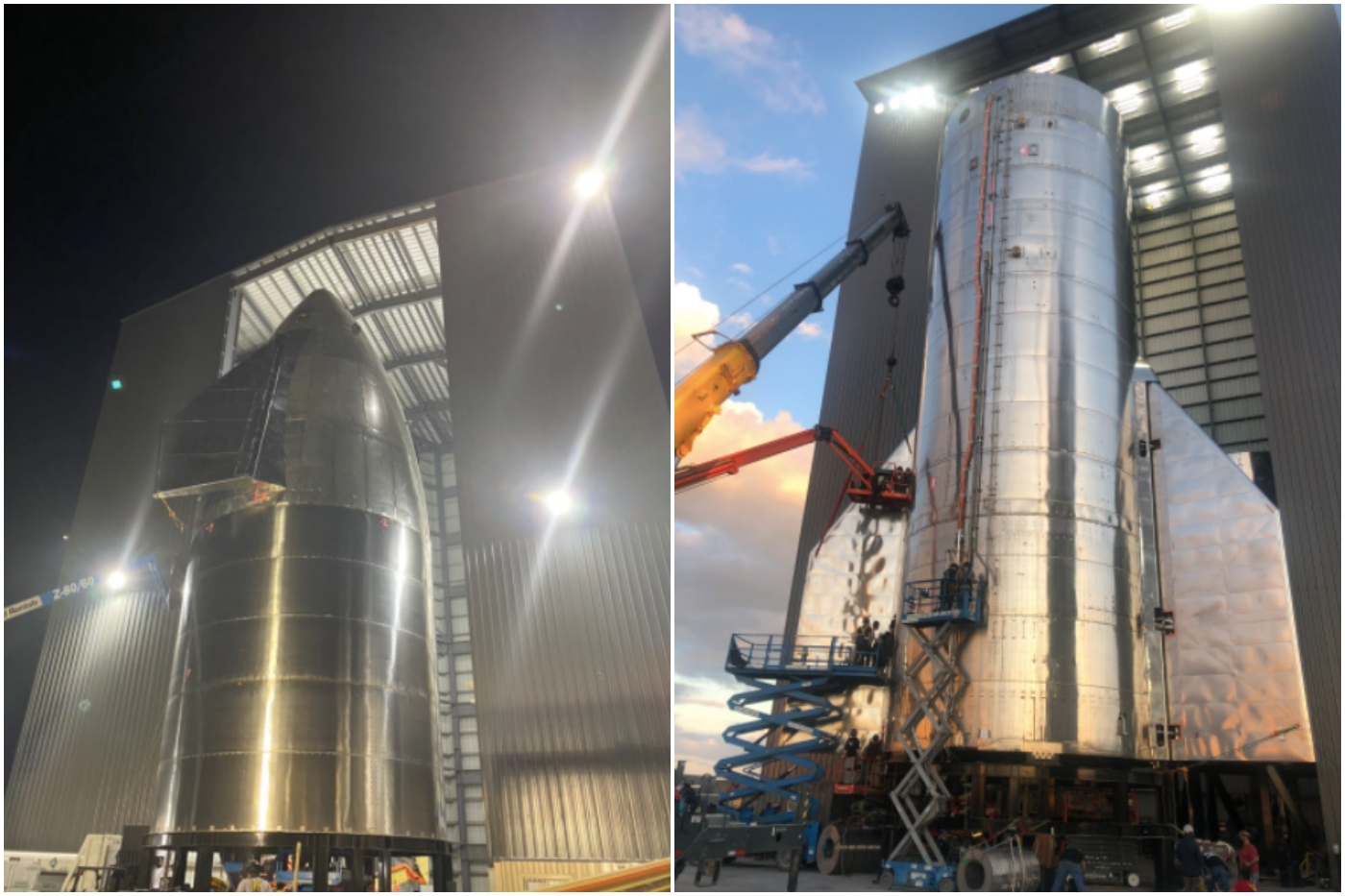
Second, the Raptor engines will relight moments before SN 8 lands, to push the vehicle to a vertical position and stabilise it. Reigniting engines and changing a vehicle’s orientation at around 60 m/s is a very complicated task. Because SN 8 is so big – 50m tall and 9m wide – the manoeuvre will also cause it to oscillate at least once, like a pendulum. To provide some assistance, engineers will mount the vehicle’s liquid oxygen header tank inside the nose cone.
Watching such a large object do a belly-flop moments before landing is surely going to be an exhilarating sight! Space X’s website is expected to share an update this week on SN 8’s launch.
In the last few weeks, SN 8 has passed some key tests – including a cryogenic test and a static fire test. In a cryogenic test, the vehicle is filled with liquid nitrogen at –196º C to exert extreme stresses on the structure, simulating the flight environment. In a static fire test, the engines are fired at full throttle while the vehicle remains bolted to a launch mount. In the coming days, there could be another such test before the test flight.
In the final analysis, given the considerable amount of innovation SN 8 represents, its test flight is likely to yield many important insights into what SpaceX can do better with the SN 9 and 10 prototypes, irrespective of how well it goes. SN 9 and 10 are currently under development at the company’s facility in Boca Chica, Texas.
But if the flight is successful, the whole mission will move a significant step closer to undertaking more challenging orbital launches.
Areeb Ali is an instrumentation and control engineer with the Alesayi Group, Jeddah.