
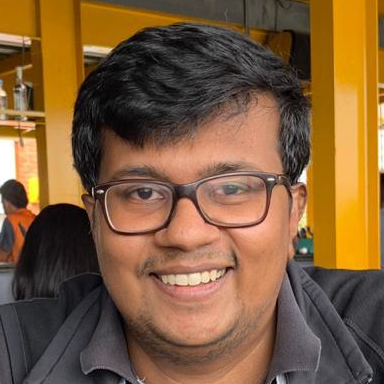
Vasudevan Mukunth is the science editor at The Wire.
The event marks the first time an indigenous cryogenic engine was used on an operational GSLV flight – but that’s not all.

This article was updated on September 8 to reflect the successful completion of the F05 mission.
ISRO successfully launched a GSLV-MkII rocket on September 8, at 4.50 pm, from the second launchpad at its spaceport in Sriharikota. The rocket carried the INSAT-3DR satellite to a geostationary transfer orbit around Earth. The mission designation was F05.
Here’s all you need to know about why this launch was an important occasion for the Indian space programme.
1. The launch was ISRO’s fourth using an indigenous cryogenic engine
The first test-flight of the GSLV with a cryogenic upper, or third, stage happened in April 2001. It was a failure. After that, eight flights of the rocket have happened over the next 14 years years. Of these, five flew with a Russian cryogenic engine onboard while the other three used the indigenously developed ones. Three succeeded, four failed and one was a partial success. The first successful test-flight using the Russian engine happened in May 2003. The first successful test-flight using the indigenous engine happened in January 2014.
2. The launch was the first time an indigenous cryogenic engine was used on an operational flight

An operational flight means ISRO will not be testing any components, flight parameters or flight routes. The launch will solely be about the mission: delivering the payload.
ISRO planned to develop a cryogenic engine for use in its rockets in 1986. In the next three years, three different entities from around the world offered to help develop these engines as well as train personnel to work with them. ISRO accepted only the third offer, from a company called Glavkosmos in the erstwhile Soviet Union, because the first two (from the US and France) were unaffordable. However, a paranoid US government imposed sanctions on India and Russia after ISRO and the Russian company refused to call their deal off upon American insistence. The most important effect of this was the Boris Yeltsin government in Russia pressuring Glavkosmos to call off its partnership immediately.
As a result, ISRO had to find its own way in the dark. The silver lining was that the company had supplied the organisation with seven cryogenic engines and one mock-up for testing at some additional cost. The indigenous engines that came later were built at the Liquid Propulsion Systems Centre, headquartered in Thiruvananthapuram. And for all the trouble it has been to build and operate, the cryogenic engine allows the GSLV to lift upwards of 1,500 kg to the geostationary transfer orbit. The PSLV rocket cannot reach this orbit with anything heavier than 1,400 kg.
3. The INSAT-3DR satellite will follow up after the INSAT-3D

The INSAT-3DR satellite continues the mission of the INSAT-3D satellite, which was launched in 2013. Both of them belong to the larger class of meteorological satellites operated by ISRO, which includes the KALPANA-1 and the INSAT-3A. KALPANA-1, INSAT-3A and INSAT-3D are in the geostationary orbit. The F05 mission on September 8 will see the GSLV-MkII launch the INSAT-3DR into the geostationary transfer orbit. From there, the satellite will use its built-in propulsion systems to manoeuvre into its eventual geosynchronous orbit.
The launch mass of the satellite is 2,211 kg. Of this, 1,255 kg is in propellants.
The INSAT-3D satellite was an improvement from its two predecessors because it possessed an atmospheric sounding system. This allowed it to map vertical changes of humidity, temperature and ozone content in Earth’s atmosphere. The INSAT-3DR will be capable of making the same measurements – as well as better image night-time clouds, and better measure sea surface temperature. And like 3D, the 3DR will also include a search-and-rescue transponder, used to pinpoint the location of distressed vessels at sea.
The 3D will operate until 2021. The 3DR will last till around 2024. A second successor, INSAT-3DS, is expected to operate from 2022 to 2029. The 3B and 3C are not operational.

4. A successful launch will have ISRO engineers more confident about the GSLV-MkIII
The GSLV is of three kinds: Mk-I, Mk-II and Mk-III. All three have a solid-fuel first stage and a liquid-fuel second stage. The Mk-I uses cryogenic engines of Russian make for the third stage. The Mk-II uses four liquid-fuel strap-on boosters in addition to the first stage and the CE-7.5 indigenous cryogenic engine for the third. The Mk-III will use two solid-fuel boosters for the first stage and the CE-20 indigenous cryogenic engine for the third. The first developmental flight of the Mk-III is expected to happen in December 2016, when it will also carry the 3.2-ton GSAT 19 satellite. A flight in December 2014 had only two functional stages – the CE-20 engine to be used on it had been under development.
The F05 mission on September 8 assumes additional significance when the Mk-III test-flight is moved into its backdrop. The Mk-II can lift payloads weighing 2,500 kg to the geostationary transfer orbit. Anything heavier and ISRO has to enlist the services of the French company Arianespace and its Ariane rocket. Specifically, the Ariane 6 can lift 6.5 tonnes to the geostationary transfer orbit. Every time ISRO uses an Ariane 6, the cost is about $95 million. Given that an Mk-II launch costs about $35-40 million, an Mk-III launch that costs between $40 million and $95 million will be also be more economical for ISRO. This benefit is sweetened by the fact that the global satellite-launching industry is estimated to be worth over $300 billion. However, it must be noted that once the Mk-III is ready, its payload capacity of around 4,000 kg to the geostationary transfer orbit will place it in direct competition against SpaceX’s Falcon 9 rocket. Each Falcon 9 launch costs around $62 million.
But the more symbolic importance is this: once the Mk-III is ready, it will make ISRO self-sufficient in terms of launch capabilities.
It only bodes well that the last two flights of the Mk-II, using the CE-7.5 engines, have both been successful. And now that the F05 mission was also successful, ISRO engineers can proceed with confidence about the prospects of the CE-20 engine*. After all, once it is fully operational and the Mk-III has established itself as reliable after multiple successful flights through 2017, the rocket will eventually be used to carry Indian astronauts to space.

The cryogenic engine is troublesome because of how it operates. One way to classify rocket fuel is as solid, liquid and gaseous. Solid fuels don’t flow but release more energy than liquid fuels. Liquid fuels do flow and release more energy than gaseous fuels. Gaseous fuels are harder to contain and don’t flow. But on the flipside, they also boast a star-performer. When hydrogen burns in the presence of oxygen, the resulting change in momentum per unit of fuel combusted is at least 30% higher than that delivered by most other practicable rocket fuels. And this is the chemical reaction that a cryogenic engine facilitates; the ‘cryogenic’ tag comes from the fact that hydrogen and oxygen are both cooled to cryogenic temperatures so that they become liquids and start flowing.
Easier said than done, as usual. The gases are liquefied by cooling them: hydrogen to -253.15º C and oxygen to -184.15º C. Because hydrogen’s density is so low, storing sufficient quantities of it requires extremely large containers. And the gases are transported in specially sealed tanks. Their loading onto the rocket is done with extra care, and go through pre-pressurisation and pressurisation phases to keep the liquids from vaporising. Normal pumps can’t move them to the engine’s combustion chamber – that requires specifically designed turbopumps. All containers have to be free of any moisture; the transport passages have to be maintained at low temperatures; special igniters have to be used to light them up; and the onboard computer has to prevent the reaction from going off too soon.
*The CE-20 will be different from the CE-7.5 in that the former will be lighter as well as be able to burn for longer.
Note: The article has been edited to correct a reference to Thursday’s launch taking place from SDSC’s first launch pad. It will actually be from the second.